Nitinol Components
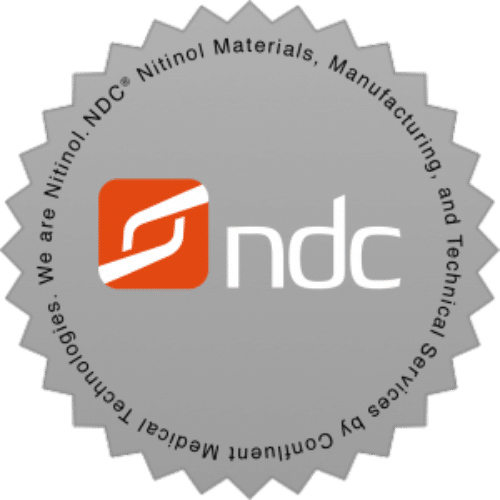
Confluent Medical Technologies, formally Nitinol Device and Components (NDC), helped pioneer the usage of Nitinol within the medical industry and we are proud to continue this legacy and expertise with our Nitinol capabilities. Confluent offers an array of Nitinol contract manufacturing services to the medical device industry. From simple and delicate wireform devices to complex and unique laser cut designs, our manufacturing facilities offer the latest technological advances to bring your most difficult devices to market.
Rapid Prototyping
- Nitinol, Stainless Steel, and Co-Cr alloy components
- Dedicated Prototyping resources including laser processing, heat treatment, electropolishing, and machine shop
- Centerless grinding
- Turnaround in 1-2 weeks, depending on raw material availability
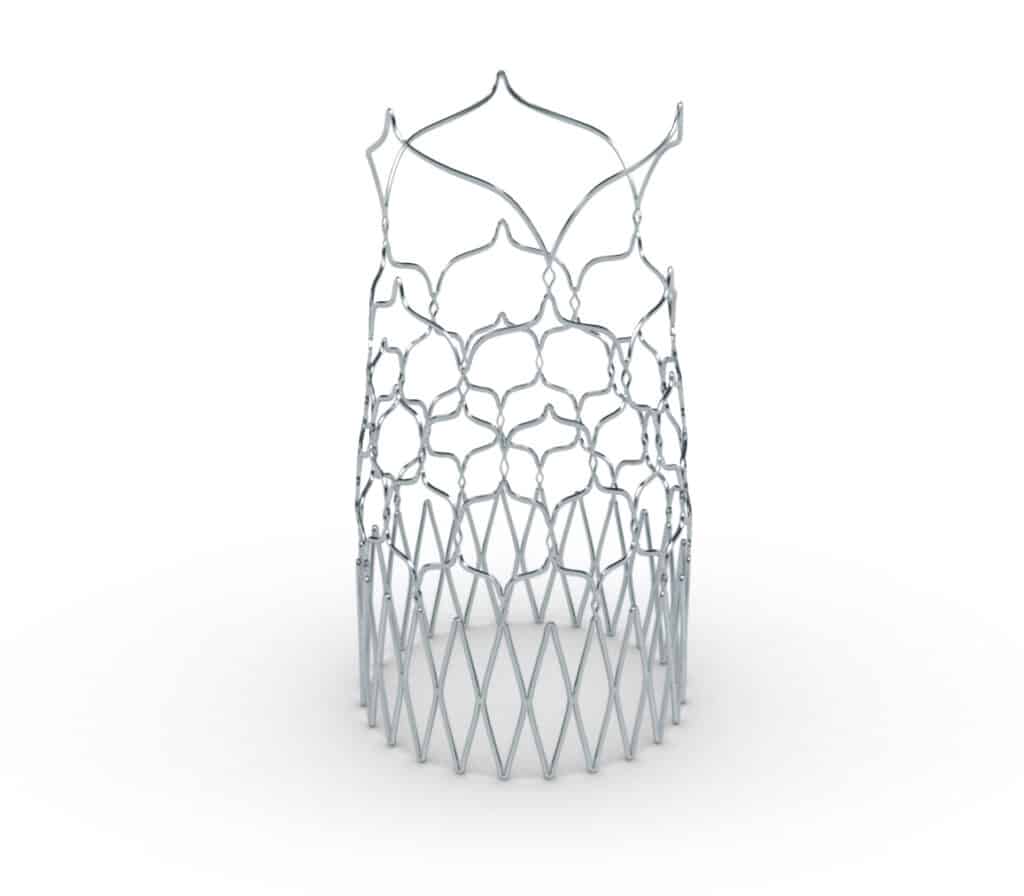
Laser Cutting and Welding
- Laser cutting and welding of Nitinol, Stainless Steel, and Co-Cr Alloys
- Tubing, sheet, and strip
- On-axis and off-axis cutting of tubing
- Fiber and Ultrafast laser platforms
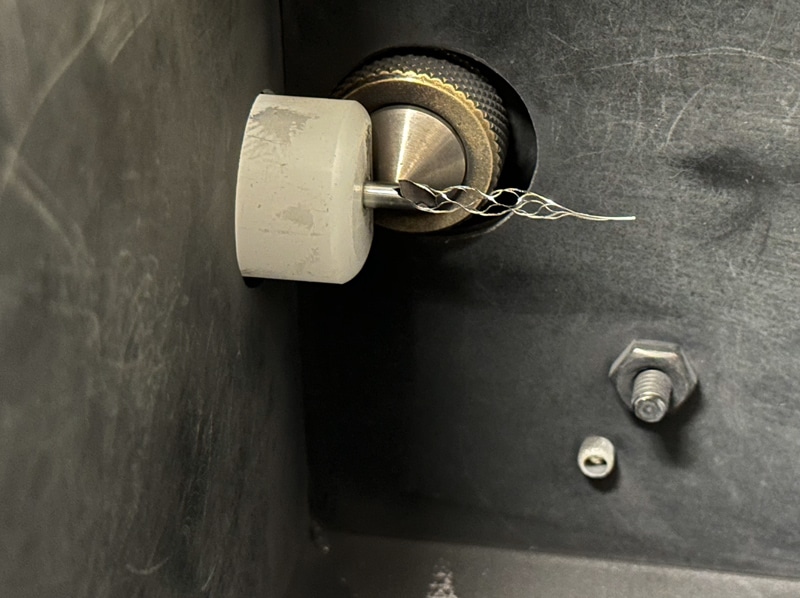
Nitinol / Metal Device Processing
- Laser cutting and welding
- Wire forming and braiding
- Profile and surface grinding
- Heat treatment and shape setting
- Microblasting
- Electropolishing and etching
- Passivation per ASTM F86 and A967
- Attaching radiopaque markers
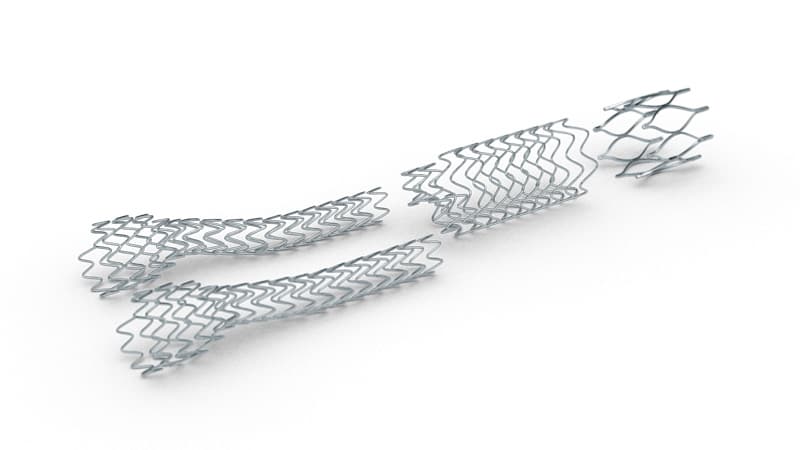
Design & Testing
- Design of implants and devices for early-stage exploration with integrated design-simulation-prototyping-testing services
- Simulation of durability and performance using finite element analysis (FEA).
- Fatigue analysis
- Crimp strain simulation
- Radial force profile simulation
- Shape-setting simulation
- Integration of simulation verification, validation, and uncertainty quantification (VVUQ) concepts
- Dimensional Metrology using optical and contact inspection methods
- Tensile testing per ASTM F2516 and E8
- Radial force testing per ASTM F3067
- Torsion testing of implants and catheter shafts
- Fatigue Testing of wires and tubing
- Kink testing per ASTM F3505
- Failure Analysis by optical and scanning electron microscopy (SEM)
- Ion Release Evaluation of Medical Implants per ASTM F3306
- Potentiodynamic and Galvanic Corrosion testing per ASTM F2129 and F3044
- Hydrogen testing per ASTM E1447
- Af Testing and Thermal Analysis of Nitinol
- DSC (Differential Scanning Calorimetry) per ASTM F2004
- BFR (Bend and Free Recovery) per ASTM F2082, both contact and non-contact methods available
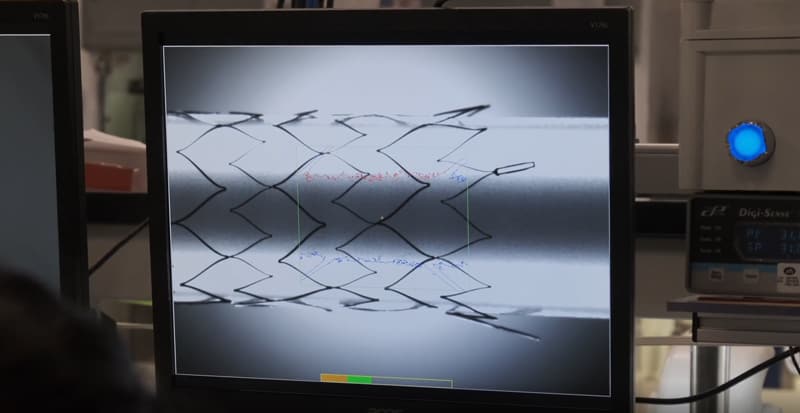
SE 508 ELI
- World’s Purest Nitinol Material
- Ideal for high fatigue applications such as Cardiovascular Implants, or small feature components such as Neurovascular Stents
- SEM images showing Microstructure comparison of SE 508 vs SE 508 ELI (both compliant with ASTM F2063)

Confluent's SE 508
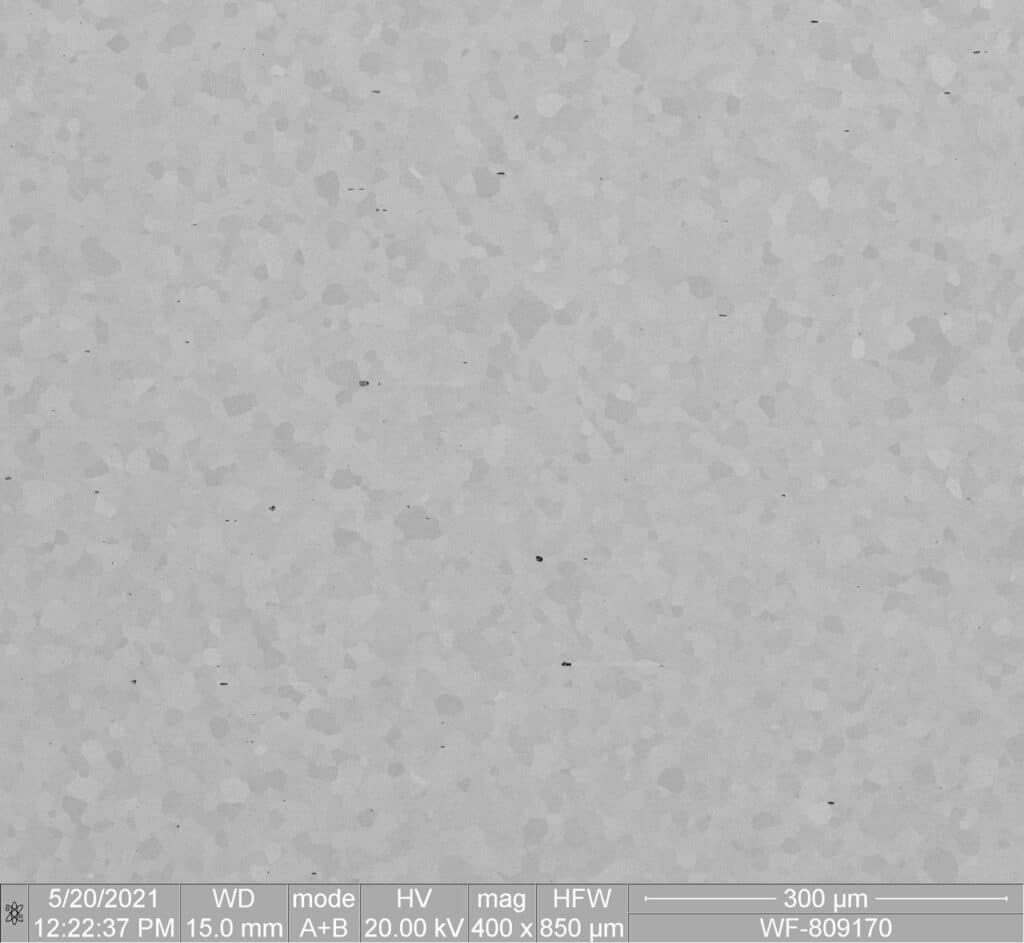
Confluent's SE508-ELI
Partnering with you every step of the way
Contact Confluent Medical today and make sure your project is supported by our unmatched resources, technical expertise and proven service to meet any design, modification or manufacturing requirements.